9 Tips For Managing And Optimizing Spare Parts Inventory
By Michael Mendoza, Hitachi Solutions
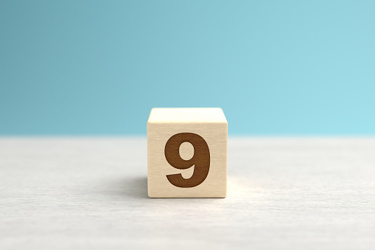
There’s nothing spare about spare parts.
Corny jokes aside, although it might seem like small potatoes, quality spare parts inventory management is imperative to the success of any manufacturer or maintenance team. After all, poor spare parts control and planning can lead to inefficient inventory storage and a shortage of parts when you need them most, which causes unplanned downtime and unforeseen costs. Therefore, for the overall success of your business, it’s in your best interest to invest in optimized spare parts inventory management, starting with these nine tips.
1. Choose a Method for Labeling Critical Components
Though it might seem obvious, it’s still worth stating: The first step to managing your spare parts inventory is to clearly label each component so there’s no question as to what’s what. This is especially important for critical components — that is, spare parts reserved for machinery critical to business operations. There are two popular methods for inventory categorization and labeling: ABC analysis and XYZ analysis.
Get unlimited access to:
Enter your credentials below to log in. Not yet a member of Field Technologies Online? Subscribe today.