The Business Case For Rugged Tablets
By Brian Albright, Field Technologies magazine
UtiliQuest learned the hard way that its mobile initiative demanded a rugged device.
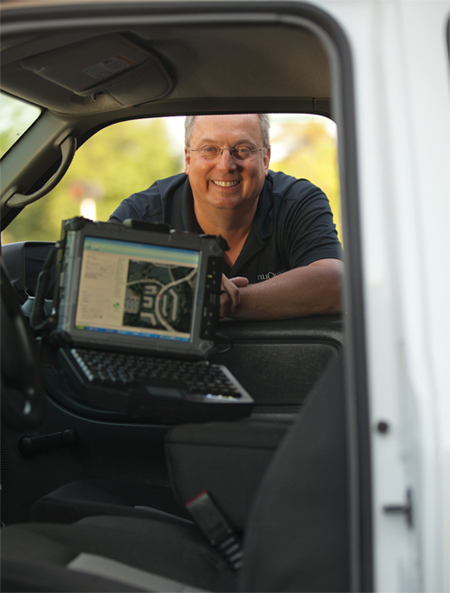
One of the biggest topics we cover today is rugged vs. nonrugged. When is rugged essential, and when is it unnecessary? UtiliQuest is one company that has successfully reached a conclusion - and its verdict is that rugged is the way to go. UtiliQuest is a wholly owned subsidiary of Dycom Industries, Inc., a publicly traded corporation that provides engineering, maintenance, and installation services for telecommunications and utility companies nationwide. UtiliQuest is often hired by utility companies to locate and mark utility lines at construction sites and has a team of 1,300 field technicians that accomplish these tasks. The company recently deployed a new field workforce management solution that combines proprietary software, rugged tablets, and GPS technology to improve the efficiency of its line location and damage inspection services, while providing enhanced documentation to its utility customers regarding their underground facilities.
Historically, the process UtiliQuest technicians used in the field was entirely paper-based. “The process of documenting the location of marked facilities has traditionally been paper- or photobased,” says Dennis Tarosky, UtiliQuest, LLC president. “This approach has been used for many years and is very laborious. It is very difficult to maintain paper-based records of literally millions of locations. Further, paper-based documentation has a high degree of uncertainty associated with it. Through the use of mobile technology, we have eliminated paper and photos, allowed our mobile workers to be more efficient, and removed the uncertainty from the data.”
Utility Customers Demand Automation
UtiliQuest sought a solution that would provide more visibility into the work being performed by its mobile workforce in real time and provide better documentation of what’s happening in the field so UtiliQuest could keep its customers informed. “Today’s client expects our industry to deliver a better service than ever before. They demand more timely information and accurate, comprehensive, and verifiable documentation of the work performed in the field. We had to find a way to provide that for them,” Tarosky says.
UtiliQuest has been able to accomplish these goals using proprietary software coupled with GPS technology and high-resolution images of the work. The convergence of mobile computing technology and GPS/GIS capabilities has enabled a host of new functionality to create new opportunities for improving the efficiency of field technicians.
However, because line location work is so specialized, Dycom, UtiliQuest’s parent company, turned to its CertusView Solutions subsidiary to develop a software solution that would improve the effectiveness of its field workforce and generate the type of documentation the company wanted to deliver to its customers. “We evaluated a number of third-party packages and ultimately chose our sister company to develop the software and hardware,” Tarosky says. “It’s a very specialized work function, and we believed CertusView was uniquely positioned to call upon the expertise of Dycom’s in-house construction and locating subsidiaries to develop and test solutions that would serve the industry better.”
CertusView developed a suite of products for UtiliQuest to use: the e-Sketch application, Virtual Manifest electronic records, the Virtual WhiteLine system, the Fieldcheck application, and OmniLume universal viewer, which rely upon a variety of geospatial and other technologies. The integrated software solution provides immediate and reliable documentation of the work performed at the job site and timely quality assurance capabilities.
Consumer-Grade Mobile Computers Just Won’t Cut It
Initially, UtiliQuest decided to roll the solution out on consumer-grade, clamshell-style laptops. However, after numerous failures of the devices — not to mention the downtime and cost associated with those failures — the company realized that deploying nonrugged devices was a mistake. UtiliQuest came to the conclusion that it needed a rugged device to withstand the environment the techs operate in and began evaluating rugged computing options. “We realized that field locating requires a very rugged device,” Tarosky says. “The old device was prone to breakage and was not as easy to secure inside the vehicle.”
On the second round of hardware evaluation, the UtiliQuest team assessed a variety of mobile computers, eventually selecting the iX104 C4 ruggedized tablet from Xplore Technologies to replace the clamshell-style laptops. Not only did the tablets provide a significantly more rugged device, but they could also be easily mounted in the technicians’ vehicles. UtiliQuest felt that the C4’s touch screen stood out among the devices evaluated as having the most easily read screen in sunlight, which is important for techs working outdoors. Further, the units have built-in Wi-Fi capabilities that help support the CertusView applications used in the field.
Once the software was developed, the company rolled out the solution to its 1,300 techs within eight months in 2009 (it swapped out the clamshellstyle laptops for the Xplore C4 rugged tablets later). UtiliQuest used its own in-house training department to develop courseware and train the technicians, taking approximately one day of classroom time to train each field office location.
GPS, Aerial Imagery Help Document Line Location
UtiliQuest uses a separate work order management solution for dispatch and scheduling, Q-Manager, which also includes electronic billing and time sheet entry. The new e-Sketch application is now integrated directly with the Q-Manager software. Technicians now wirelessly receive their assignments for the day on their iX104 C4 tablets. Typically, utilities have anywhere from 48 to 72 hours to complete their line locating work once they are notified of a dig. Q-Manager has all of these constraints loaded into its scheduling engine, so technicians can see which assignments take priority as they set up their daily schedules.
Once on-site, field technicians use a locate device (sort of a high-grade metal detector that uses electrical currents) to locate any buried utility lines or other assets. After the lines are marked with paint, the technicians return to the truck to complete the work order using Q-Manager on the tablet, which includes a link to the e-Sketch application. The e-Sketch application allows a technician to complete a detailed electronic sketch of the work performed on a high-resolution image displaying the location of the paint and/or flags placed on the ground. “Previously we used pencil and paper to manually draw a depiction of where the paint and/or flags were placed,” Tarosky says. “Using the aerial imagery available on the tablet, the technician represents what they marked on a high-resolution image of the work site using a stylus. All of the landmarks and buildings are on the high-resolution images, which become permanent reference points. These capabilities provide much better visibility for us into what’s going on in the field and also enable us to share that information with our customers.”
Upon completion of the Q-Manager and e-Sketch process, the technicians must sign the permanent Virtual Manifest record, utilizing the stylus and touch screen capabilities of the Xplore tablets. The completed work order is then saved, and the information is transmitted over the air to UtiliQuest’s central servers. The company then has an accurate record for reporting all completed location work orders to their utility customers. The utilities, in turn, can utilize the e-Sketch information internally, if they choose to do so.
Technicians have the ability to complete the work order either inside or outside the vehicle. When using the tablet outside the vehicle, “our e-Sketch application has functionality that works in concert with the GPS technology in the tablet to do what’s known as ‘follow me’ marking,” Tarosky says. “The technician can walk the site and the Xplore tablets communicate with the e-Sketch application to document where they are.”
This automated process has transformed the way the field techs work. “Eliminating paper has improved our efficiency while providing more meaningful and accurate records. Our mechanized suite of tools gives us the capability to evaluate, exchange, and share information which is dramatically different from what we were doing before,” according to Tarosky. “The technology has allowed us to really improve our service delivery and efficiency.”
Tarosky says, “In the past, employees did not have a process that allowed them to submit their paperbased work documentation until they returned to the central office. With a mobile workforce, this could take several days or even a week to accomplish. We are required to maintain millions of records for years, which previously was very costly and inefficient. Electronic transmission and storage of these records is much more timely, efficient, and accessible than the old manual process.”
Taking Your Mobile Solution To The Next Level
UtiliQuest has not finished innovating. Sister company CertusView has also developed an electronic marking wand for the company’s application which connects to the Xplore tablets using Bluetooth wireless technology or the USB port. The marking wands have embedded GPS that allow them to capture the position of the paint/flag marks as they are being placed. The detailed location of paint/flag placements is then transferred from the wand to the e-Sketch application via the Bluetooth or USB connection. This further automates the creation of high-quality and comprehensive job site documentation without the tech even having to draw lines with a stylus.
UtiliQuest has also been working on solving a challenge that faces the industry on how to inform the field technician of facilities in the excavation area prior to performing the mark-out. “It has been rare for a technician to know with certainty what they should look for at the proposed construction site,” Tarosky says. “Generally, there is not a clearly defined predetermined scope of work, so it’s a very difficult process to manage. Tools have not been available to the excavator or the locator to specifically delineate the proposed excavation area or the marked area in the past. This has resulted in needless follow-up calls, excessive and unnecessary areas being marked, and nonproductive remark efforts in order for both parties to have comfort that facilities are being protected.” CertusView has developed additional software solutions to define the excavation area, as well as document the existence of customer facilities within the proposed excavation area.
With a customized software solution and the rugged tablets the company found were necessary to support it, UtiliQuest has not only eased the burden of its field technicians’ daily duties, but also upped the ante on the service it provides. “The solution provides us valuable real-time visibility into the work that we perform. We are now able to provide a higher level of service to our customers,” Tarosky says. “And we won’t stop here. We are constantly looking for opportunities to expand the use of the technology to further automate our business and help our customers.”
The Importance Of Seeing Clearly In The Field
While UtiliQuest was able to look within when it came to developing a custom software solution for its facility location work, hardware selection wasn’t so cut-and-dry. Having first deployed consumer-grade laptops in the field and experiencing some pain from doing so, the company decided a rugged device was imperative. To find the right rugged device, UtiliQuest evaluated a number of manufacturers. Ultimately, the company selected the iX104 C4 tablet from Xplore Technologies (the newest version of this product is the iX104 C5).
According to Dennis Tarosky, president of UtiliQuest, the Xplore tablets were selected because the 10.4-inch AllVue Xtreme XGA display could be easily read in sunlight, and the device was rugged enough to withstand rough treatment in the field, including the exposure to heat and moisture it will commonly encounter. In fact, the C4 can withstand operational 4-foot drop to concrete and operational 7-foot drop to plywood, is fully submersible for up to 30 minutes, and can operate in minus 4 to 140-degree temperatures. The C4 also included a built-in camera, onboard Wi-Fi and Bluetooth, along with wireless WAN and GPS support — characteristics that were crucial to some of the plans UtiliQuest had for peripherals down the line.
And unlike the laptops that technicians previously carried, the Xplore tablets are secured in the vehicle when the technician is driving. “We are very concerned about the safety of our employees, and eliminating hazards of unsecured objects in our trucks is important,” Tarosky says. UtiliQuest was able to use rugged vehicle mounts from RAM Mounting Systems to keep the devices locked in place. RAM manufactures powered dock and mounting hardware specifically for the Xplore iX104 series that includes locking knobs with a paddle release and accessible port replication. The mounts not only dampen shock and vibration while the vehicles are moving, they also keep the tablet safely in place so that technicians aren’t distracted by a device rolling around in their vehicle. For more on Xplore Technologies, please visit www.xploretech.com.