Securing Against Supply Chain Risk
By Spencer Gisser, VDC Research
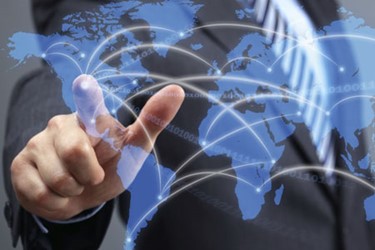
Spare parts inventory management always has been an issue for field service organizations when dealing with on-site repair. Not having the right parts at the right time can prevent field service technicians from completing their jobs, which would require repeat visits and could cause operational downtime. However, storing excess inventory comes with its own costs, and it is often difficult to minimize inventory without running low on parts. This has been exacerbated by supply chain problems brought on by COVID-19, and many field service organizations have felt the effects of running low on parts necessary to conduct repairs. COVID-19 has exposed field service organizations with poor supply chain management to serious risks such as running out of essential components.
Even though spare parts inventory management is a useful tool for ensuring that technicians have the right parts for each job, field service organizations must now also pay attention to the supply chain. Manufacturers have shut down, causing shortages of parts necessary for field service operations. According to a report by Fortune, 94 percent of the Fortune 1000 have seen supply chain disruptions caused by the coronavirus. In Q1, the impact was most acute for manufacturers in the APAC region, while late Q1 and Q2 saw this phenomenon extend to North America and Europe. However, manufacturers in APAC have begun to reopen and resume manufacturing capacity. As more countries continue their efforts to combat this virus, manufacturing will hopefully begin to pick back up elsewhere in the world.
While no one prepares effectively to contend with once-a-century pandemics like COVID-19, companies with the least visibility into their operations and supply chain are faring the worst during this downturn. These field service organizations risk running low or running out of parts, failing their customers, and affecting their operations. Ultimately, understanding the condition of the supply chain is essential to predicting future availability and taking action to preserve it.
There are three main actions that field service organizations can take.
Be Proactive With Your Supply Chain
As everything about this pandemic has proven, no one knows what the long-term outlook will be with any real certainty. Some regions are beginning to open back up, but this may very well be premature. To guard against the risk that coronavirus’s effect on manufacturing will endure, field service organizations should order parts now and stock up. Even though prices may be higher than normal, prices may continue to increase over the pandemic’s duration.
Find new suppliers to provide the parts and equipment you need. This way, if one of your suppliers is forced to suspend their operations, your organization will have the flexibility of relying on other suppliers to fill the gap.
Stay In Touch With Your Customers
Given the many disruptions of the coronavirus, your customers’ operations may change for some time, causing demands to rise or fall depending on their sector. Understanding your customers’ needs can help you plan for what supplies you will and won’t need going forward. The distribution of the spare parts you want to have on hand may be different from what you expect.
Consider Adopting A Supply Chain Management Solution
Field service organizations can use supply chain management solutions to support part sourcing from multiple vendors and can monitor and account for a wide variety of informational areas. Parts forecasting can entail the investigation of many factors including historical data, causal effects, and understanding connected information. This element alone can draw from many data sources. In terms of sourcing a given item, there are many options that include getting the item from another location, repairing a broken or worn item, upgrading an out-of-date item, and building or buying a new one. Each of these options may entail different costs and time requirements that can depend on anything from the weather to fluctuating material prices. Optimization engines geared toward supply chain management can help organizations create an optimized part mix to manage various types of risk.
About The Author
Spencer Gisser is a market research and consulting professional within VDC’s Enterprise Mobility and Connected Devices practice, supporting both syndicated research and custom engagements. Before joining VDC, Spencer conducted in-depth market analysis at cybersecurity company Covata. Spencer also founded and moderates /r/Security, a 134,000-person online forum enabling the cybersecurity industry. Spencer holds a B.A. in Government from Harvard University.