Mastering Spare Parts Inventory Management To Reduce Fleet Downtime
By Emily Newton, Revolutionized
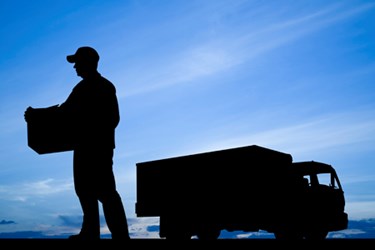
Efficient spare parts inventory management can help reduce downtime in your fleet due to challenges like shortages, out-of-stock parts, lengthy repairs, and more. Poor inventory management can leave your team without critical equipment for completing maintenance as quickly as possible. A lack of reliable spare parts can even lead to more frequent breakdowns.
You can prevent situations like this using innovative spare parts inventory management strategies. These tools and tactics will help you ensure your maintenance team always has the necessary equipment to keep your fleet in top condition.
Use An Inventory Management System
One of the most effective strategies for reducing fleet downtime is utilizing an inventory management system (IMS). This virtual platform automates the process and makes it easier to view accurate levels. An IMS can track spare part quantities, give low-stock notifications, monitor component usage, and more.
Choosing a good inventory management system for your fleet can be overwhelming initially, but it’s all about focusing on your team’s needs. There are a few main features any inventory management system should have, such as a user-friendly interface, a fair price, and low-stock notifications.
If you’ve never used an IMS before, it may be helpful to consider the challenges you are currently facing with managing spare parts inventory. For example, you might have trouble keeping track of part usage, leaving your team surprised when they run out of something. In this case, look for an IMS with a user-friendly interface and good monitoring and low-stock notification features.
Likewise, you may have a large team or fleet, making managing the sheer quantity of spare parts and repairs challenging. In this case, an IMS with plenty of automation features would be beneficial. It can streamline your inventory management so you don’t encounter downtime due to lengthy manual processes.
Track Repairs And Inventory Usage
Regardless of what type of IMS you use, prioritize tracking repairs and inventory usage. Monitoring this activity helps ensure good maintenance practices and also will help you build a valuable data set on spare parts consumption.
Over time, inventory usage data can show you what spare parts your technicians use most often and what they’re using them for. You can use this information to predict future demand. Demand forecasting is a great way to keep from running out of important components and gives you extra time to get ahead of supply chain delays.
Inventory usage also will reveal what parts need to be replaced most often, which may indicate a root cause you can resolve. For instance, you might find that your technicians are replacing brake pads excessively often. This could be due to an issue with the specific kind you are ordering or certain driver behaviors. Identifying and recognizing the problem lets you address it and reduce downtime for repairs.
Create A System For Field Repairs
One of the leading causes of downtime is emergency repairs in the field, such as a dead battery. Stocking vehicles with spare parts for minor fixes can significantly reduce downtime and related costs. For example, instead of waiting for a tow truck and paying for its services, a driver or technician can perform the repair using components they have with them.
To accomplish this, you must determine what spare parts your drivers would most likely need for emergencies. An inventory management system or repair data is a big help in this process. You also can survey your drivers and ask what tools and parts would help them in the field.
Remember, some repairs are too large-scale or complex for a driver to complete independently. So, focus on spare parts for basic fixes a single person could do without specialized equipment. Additionally, create a system for tracking field repairs to keep components in stock for on-board repair kits.
Automate Restock Notifications
Lengthy maintenance timelines are a common cause of fleet downtime. Various factors can cause delays in the process, including a lack of the right parts. Poor inventory management can increase work stoppage by forcing repair technicians to wait for new components.
Luckily, it’s fairly easy to prevent situations like this. An inventory management system can automate inventory monitoring and restock notifications. In the IMS, set a minimum stock level for each part and ensure your team updates it when making repairs. With accurate tracking, the IMS will notify you well before you run out of important components.
Automatic restock notifications also allow you to get ahead of supply chain disruptions. Many fleet managers continue to face delays and shortages of critical maintenance equipment. However, you can reduce the impact of supply chain issues if you leave yourself time to pivot or adjust.
For example, you can shift to online platforms or new brands to source spare parts. Transitioning from a particular supplier that is frequently out of stock can help you get a better price and avoid downtime due to shipping delays. Many fleet managers also find it easier to connect with new suppliers through online marketplaces.
Use Data Analytics To Predict Demand
Restock notifications are one component of a larger inventory management strategy: demand forecasting. The information you collect is invaluable for predicting future spare parts demand using data analytics. This is especially true if your team’s repair needs fluctuate throughout the year.
There are a few ways demand forecasting can reduce downtime. First, it allows you to order spare parts weeks or months before you need them. Submitting orders early is crucial for minimizing the effects of any supply chain delays.
Demand forecasting also helps you anticipate the types of repairs your team will need to do throughout the year. You can use this information to prepare your technicians using training or refresher courses, including learning where to find the necessary spare parts and how to use the IMS. This minimizes the likelihood of downtime due to technician errors or confusion.
Minimizing Downtime With Smart Inventory Management
Spare parts inventory levels play a vital role in preventing maintenance downtime. Even if your team is fully prepared for a repair, they may be unable to finish it quickly if they don’t have the right items.
Ensuring you keep essential parts in stock, monitor inventory levels, and accurately anticipate future spare parts demand is crucial. Fleet managers can accomplish this by using an inventory management system, tracking part usage, providing components for emergency repairs, utilizing automation, and analyzing data.
About The Author
Emily Newton is the Editor-in-Chief of Revolutionized. She regularly explores the impact technology has on the industrial sector.