Industry 4.0 And The Customer Experience
By Jeff Oskin, Jolt Consulting Group
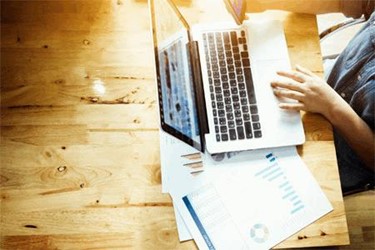
The fourth revolution in manufacturing is here, and it’s not only reshaping the way things are made but also evolving the customer experience. Dubbed Industry 4.0, this fourth major upheaval in modern manufacturing, follows the lean revolution of the 1970s, the outsourcing phenomenon of the 1990s, and the automation that took off in the 2000s. Today’s digitizing of manufacturing will take what was started in the third industrial revolution with the adoption of computers and automation and enhance it with smart and autonomous systems fueled by data and machine learning.
By moving beyond the use of computers to cyber-physical systems, the Internet of Things and the Internet of Systems, Industry 4.0 is making the “smart” factory a reality. Leveraging reliable cloud computing, advanced robotics, and lower-cost 3-D printing, Industry 4.0 can utilize these components to optimize manufacturing. Decisions can now be made without human involvement, and as a result, machines become smarter over time as they access and share more data across their network. The goal is for the smart computers to improve efficiency and reduce waste.
Access to this data also has a direct connection to the customer experience. Through gathering more data and making better use of analytics, smart factories can provide greater insight. Examples include order statuses on a manufacturing floor and maintenance needs, identifying patterns, and giving the manufacturer better control and visibility to make decisions on aligning resources.
Much has been made within the service world of connected devices and their impact on servicing customers. Monitoring equipment in real-time and using readings to drive downstream service activities has long been the vision of “connected service”. Adoption within service, however, has been slow, largely due to a lack of perceived value as well as immature technology infrastructures across most service organizations.
The concepts driving Industry 4.0 may be the impetus necessary to make connected service a reality as it expands the value equation beyond the service department to include other core facets of an enterprise (e.g. manufacturing). This broadening of scope results in an improved business case, thus increasing the willingness to make the necessary investments. Industry 4.0 also broadens the connected service vision. More specifically, it expands the vision from equipment being remotely monitored by a service department for the purposes of predicting faults or reducing downtime to include additional value for a customer, such as providing real-time views into an order as it progresses through the production floor
Although some executives may be skeptical about this next industrial coming of age, Industry 4.0 is gathering force. Executives should begin preparing for the digital transformation by investing in digitally ready technology infrastructures and developing strategies to upgrade their processes to support the coming change. Additionally, executives can begin assembling the best talent and determine how to structure their organization as Industry 4.0 gathers steam. They should ask the questions, “Which data is the most beneficial?” and “Which absent data points cause the most pain?” to collect and analyze the information needed to operate most effectively.
About The Author
Jeff Oskin is the President of Jolt Consulting Group LLC. He is an expert understanding business visions and translating those visions into concrete action plans that organizations can execute. He has proven countless times throughout his 20+ year career an ability to be a savvy executive who understands the nuances of optimizing business operations, managing change, acquiring technology and managing large-scale programs/projects.
Sources
https://www.mckinsey.com/business-functions/operations/our-insights/manufacturings-next-act