How to Upfit Your Field Service Company's Trucks
By Joe Birren, Merchants Fleet
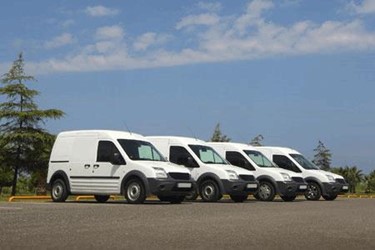
Operating with the proper equipment is crucial when it comes to running a successful fleet. By upfitting your company trucks the right way, you will watch your business transform to reach new heights — and with careful research and the help of an upfitting partner, you can optimize your fleet’s production in the field service industry.
Wondering if upfitting is a viable option for your business? Read on for an extensive guide about how to upfit your work trucks for the field service industry.
Field Service Truck Basics
Let’s start by covering the key aspects of field service and what makes it important. Field service is classified as 24/7 service that is available on the job site, meaning that any services that can be performed in the shop can be performed right from the truck. Doing so can lower business expenses, reduce inactive time, and keep on schedule more efficiently. These services, performed by a field technician, may involve the installation, maintenance, or repair of hardware or equipment. Common industries in which field service trucks are needed include companies in the automotive industry such as AAA or the industrial industry such as HVAC or plumbing companies. Other examples include companies in healthcare technology such as emergency responders and the telecommunications industry such as Comcast or Xfinity.
Depending on your business, field service can either be an additive or a necessity. If your business uses large equipment such as bulldozers, cranes, or excavators, it is more feasible to conduct on-site repairs rather than transport. Another reason you would need to use field service is a situation where it would do more harm than good to move the equipment from its current location, such as engine damage. Lastly, your business might need field service if you have a packed schedule in which you cannot afford to have a particular machine out at one repair for an extended period.
Where To Start?
The first step of the upfitting process is to determine your specific field service equipment application and payload requirements. Depending on the industry that you are operating in, these needs will vary widely. One of the first considerations to make is whether you decide to buy or lease your work truck, as this factor can change how you upfit your vehicle. There is a multitude of upfit options regarding truck appearance, storage, safety, and equipment usage. For example, a field service technician will require a bucket truck because he/she must be able to install, maintain or repair all forms of telecommunication lines. On the other hand, a mechanic technician will require a truck that is equipped with features ranging from a variety of tools, an onboard air compressor, welder and diagnostic testing equipment, and a crane. A mechanic’s truck also will require an inspection, and there are different inspection checklists for field service trucks in each industry. It’s helpful to work with a team of experienced truck & upfit engineers, who can provide consultative services to ensure the correct vehicle is spec’d for the correct application.
Additionally, it is important to make sure your upfit needs align with your budget and timeline. A major hurdle will arise if the vehicle is built to your budget but does not meet the performance expectations such as load capacity and safety. Be realistic about your timeline for upfitting and remember to consider future instances such as additional costs or unexpected occurrences.
Choosing the Vehicle Body & Upfits
Once you paint a clear picture of what your needs are, the next step is to pick your vehicle body and specific upfitting features. Common examples of upfit features range from ladder racks, bulkheads, and anti-slip flooring to cranes, cargo floors, and more complex electrical equipment. Again, this will all vary by your business’s unique needs. For example, a telecommunications truck will undoubtedly need a boom lift, whereas a roadside service truck will not. In any case, it is important to ensure that the truck possesses a service body that will fit all of the necessary tools.
You will want to choose features that will make access to equipment easier for the truck driver. If you know that a truck driver uses the battery reader regularly, it is best to keep it in an accessible location such as the side compartment in the truck cap. Similarly, vans with roof racks or ladders will better suit a cable repair company rather than a standard pickup truck would. Other common upfit features that might be helpful include floor drawers, hitches, ramps, and fold-away shelving.
As for safety measures, another notable consideration to keep in mind is the gross vehicle weight rating. GVWR is defined as the maximum total safe weight of your vehicle according to the manufacturer’s specifications. GVWR includes the weight of the vehicle plus the maximum allowable weight for occupants, payload, and equipment that the vehicle can legally handle.
Popular Fleet Vehicles For Field Service
- Bucket Truck. A bucket truck is fitted with a hydraulic articulating boom that includes a bucket at its end for the technician to stand in. The boom lift of a bucket truck is practical for telephone line repair workers because it permits service bodies to fit all of the necessary tools on the outside of the truck. The operational working height and type of boom are two of several critical factors when spec’ing a bucket truck. It’s highly recommended to spec an insulated boom, when possible, for added safety when working around any electrical equipment and increased residual value.
- Sprinter Vans, High Clearance Vans, & Cargo Vans. Created by Mercedes Benz, a sprinter van is ideal for field service industries that require the use of a significant number of tools. In these trucks, technicians can comfortably stand up and seek what they need easier. These vans are also fitting for technicians who perform their work in the van, such as HVAC or service technicians, locksmiths, and even dog groomers. Cargo vans are best suited for industries in which the technicians will not be working inside the van itself, yet still must fit a large number of tools. These vans are often used by mobile businesses such as carpet cleaners or chimney sweepers.
- Minivans. Minivans come in a wide variety of sizes, thus providing countless options to meet your needs. Opting for a smaller-sized minivan will be better for fuel economy and can even help drivers who service heavily populated cities with uncertain parking situations. One of the best features of minivans is their compact size for heavily populated metro areas where parking can be challenging.
- Pickup Trucks. The bed of a pickup truck offers extremely easy access to tools and equipment, ensuring a smooth loading and unloading process. A pickup truck will allow you to put a variety of storage solutions either in or on the bed, making it even more customizable. When deciding, we also recommend asking your employees what would help them do their jobs more efficiently. This is a great way to get additional information on what solutions are an absolute must and where there could be room for improvement.
Consider Working With A Fleet Leasing/Management Company
A good way to ensure your upfitting process is smooth and stress-free is to work with a knowledgeable fleet leasing company. Having a trusted, reliable partner in your corner throughout the upfitting process can provide you with ease of mind that you are making the best possible decisions for your business, your employees, and your customers. Moreover, it is a great option for fleet managers who are tight on time. A fleet leasing company will work closely with all parties involved to aid your fleet in reaching peak efficiency.
Upfit Timing Is Key
When it comes to upfitting, timing is crucial. You should conduct extensive research on the ever-changing specifications and plan ahead, as the process can often take a long time. Be sure to know when you need vehicles in the field and consider how you will keep your field service business running smoothly while embarking on the upfitting journey.
4 Additional Upfitting Tips
In addition to these essential steps, here are four more tips to keep in mind throughout the upfitting process.
- Keep safety in mind with the new upgrades.
- Always consult the drivers/technicians when planning upfitting; they are the people who will be working hands-on with the upgraded work trucks.
- Keep budget in mind.
- If multiple drivers use the trucks, efficient storage can help cut down service call times and confusion.
If you operate within the field service industry and wish to obtain more efficient production, upfitting your trucks might be a great option to pursue. With the wide array of existing fleet vehicles and upfit options, we are certain that you can find a solution that will meet your fleet’s unique needs. Start by taking the steps to optimize your fleet’s equipment and watch your business begin to flourish within the field service industry.
About The Author
Joe Birren serves as the Fleet Operations Manager for Truck and Upfit Engineering at Merchants Fleet. He has over 20 years of industry experience managing the upfit process and ensuring clients have optimized designs to meet the needs of their fleet. Merchants Fleet’s ASE-certified truck & upfit engineers are available for consultation or, when needed, to provide a site visit at your location to better understand your application and payload requirements. For more information, visit merchantsfleet.com.