Fielding IoT Advantages For Field Service Technicians
By Michael C. Skurla, Chief Product Officer at Radix IoT
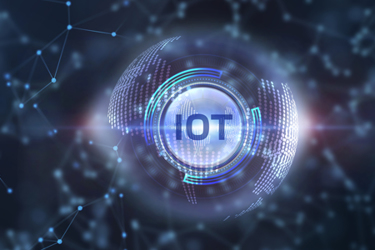
Imagine this scenario. You receive a call from a tenant in a building that the heat isn’t working. Simple enough, you deploy a field technician to troubleshoot the issue. The drive is 3 hours away. Upon arrival, they spend a few hours looking over everything to find a simple, defective thermostat. Sadly, it’s a manufacturer specific thermostat that is not on the truck. A call to the central office sends a flurry of confusion, which trickles to a purchasing agent, a distributor, and finally an order for a new thermostat, which is in stock in Jacksonville, Florida. The problem is you’re in Seattle, Washington.
Next day the thermostat arrives, the technician goes to get the thermostat from the shop and makes the three-hour drive again–six hours round trip. Overall, two to three days of repair time, countless hours commuting, and expedited shipping. Simply put, this is not the way to service a customer left without heat and stressed–not to mention the expense and all these issues could be addressed with more intelligence in monitoring and management.
This has become even more acute in our COVID world, where working and living become one activity, and uninterrupted living and connectivity become a 7x24 necessity.
It is not revolutionary, but incremental operational change to embrace a technology that allows for a much more streamlined experience. Let’s revisit our above example.
Your service organization has deployed a basic remote monitoring and management solution using an IoT platform as its basis for customer monitoring. Devices at the ‘Edge’ (the building in this case) are communicated with from the IoT platform to verify functionality at a regular interval. On Saturday, the platform dashboard alerts that the thermostat has stopped responding. A work ticket issued to procurement to order a new sensor is followed by a subsequent ticket to roll a truck once the sensor has arrived on the same day. In the meantime, an alarm is created in the system and an email sent to the customer explaining the detected problem and actions taken to address the issue. A remote technician also logs into the system and sees that it’s possible to override the thermostat by communicating via the BMS system, and programs a temporary set-point to maintain a working temperature while the problem is resolved over the next few days.
Out of these two scenarios, which will an end-user or customer be more apt to renew their service contract with? The answer is clear. No panic calls, no ‘out of the loop’ angry customers threatening to cancel their service. The scenario is not fiction. It’s real, and it’s in practice nationwide and across the globe in critical facilities. It belongs, however, far beyond situations where seconds matter. Datacenters and telecommunications companies have been doing this for decades, but it’s not exclusive to the realm of hi-tech. Apartment complexes, commercial offices, retail, and homes all can benefit from this –regardless of how many sites need to be managed or monitored. And it is staggeringly affordable compared to the alternative, typically using existing technology.
The greater demand for always-on connectivity has increased the critical role of connectivity with the Edge (an I.T. centric word for a building or location). This dependence on 7x24 connectivity and operations continues to increase in our highly connected world across all industries. What was once classified as ‘critical facilities’, referring only to data centers, is now relevant to most every facility. Working is now possible from everywhere and no longer limited to offices or commercial structures, but at coffee shops, homes, and retail establishments at large. Why can’t these sites offer the same reliability as those sacred data centers or other establishments? Staffed or unstaffed locations alike, urban or remote, businesses, individuals, and consumers are unwilling to put up with perceived downtime. There’s nearly no tolerance for failure or service inadequacy.
IoT Platforms Are Fielding To The Edge
Organizations have been advancing their competitive edge for years with various forms of automation and software tooling. Yet, it has been difficult to achieve this level of reliability with multiple existing vendors or technology in a single space, and even more complex when this technology spans generations of equipment. More recently, organizations have been adopting Internet of Things (IoT) solutions, and specifically IoT platforms that remove this complexity of generations and vendors. IoT frameworks and platforms offer an ecosystem that rationalizes data across existing equipment and platforms to offer a cohesive clean slate of data from all devices to enable actionable insights.
It’s estimated there will be 75 billion IoT devices online by 2025. These communicate via multiple mediums, but Cellular IoT connections are expected to reach over 3 billion by 2026 as the technology grows more popular, according to new data from ABI Research.
This seamless automation of all the connected devices generates a ton of data points as the devices talk to each other and to the outside environment–with no human involvement. An IoT platform makes this data useful and actionable by aggregating, organizing, and storing this disbursed data into logical structure so it can be mined easily into actionable insights that the command center operators and managers can use to link to their field service technicians, predictive analytics tools, and more.
This level of seamless connectivity from the central command center to the field technicians allows the flow of real-time data regarding repair needs, scheduling, sequences of operations, and other time-consuming field service tasks. Using these platforms, technicians can diagnose a problem while operators can alert the right technician to handle the problem–organizations save money and time with full flexibility and efficiency since automated and supply chain integration are possible–all of which enable the field force to be as effective as possible in real time.
Interestingly, IoT platforms are seamlessly integrated and up and running in no time. A common misconception is that to gain this level of monitoring, you need to replace a lot of the existing infrastructure. Nothing is further from the truth for IoT platforms. Their tenant being they sit on top of existing systems and allow for a single source of truth for all data generated across those systems, that otherwise would require separate software and operators for each individual trade in a building. IoT platforms enable operations efficiency at every level.
Given that IoT platforms are based on I.T. standards and not just smarter BMS/EMS solutions that secure remote connection, they enable remote management of thousands of locations, positioning them as a natural choice to integrate what was previously considered non-integratable. The empowered remote management capabilities of IoT platforms are easy to use and deploy, and all based on I.T. standards, and not custom ad hoc solutions.
IoT Streamlines Field Service
The vast interconnected ecosystem made possible by cellular technology and that of the emerging 5G world enables all service organizations and their respective field technicians to be fully connected in real-time, not only to their headquarters but also to their equipment via mobile devices. Not all are very affordable. Full automation via IoT platform keeps the pulse of all connected equipment and drastically reduces human error.
Whether via phones or iPads, field technicians expedite the response time to all service requests. IoT connectivity and automation means increased customer satisfaction with expedited, proactive response time. With risks mitigated, this connected workforce allows field technicians to be an extension of the sites they manage and monitor with full access to all the reporting abilities.
IoT platforms’ single pane of glass provides a unified trusted truth, allowing operators to remotely monitor and manage critical facilities’ equipment across geographically distributed locations. Business continuity, maintained by data acquired from the IoT platform feeds analytics, allows for preventative maintenance, eliminating costly downtime, and diverting major risks in real-time, all while working with existing infrastructure and software tooling. The remote triage capabilities can drastically decrease operational costs, particularly when blended with procurement.
The most stunning part of IoT platforms is their ability to adapt to an organization’s specific business needs and change as needed to meet evolving monitoring or control requirements and provide top outcomes without expensive or elaborate software projects.
Enabling the maintenance of operations and integrity of facilities remotely, make IoT platforms indispensable tools for remote monitoring and management of critical infrastructure. The rapid provisioning abilities of IoT platforms allow newly deployed facilities–locally, nationwide or across the globe–to be fully connected to their field technicians for seamless operations while remaining efficient, cost-effective, and relevant into the future.
---
Michael C. Skurla is the Chief Product Officer of Radix IoT– offering limitless monitoring and management rooted in intelligence–and has over two decades’ experience in control automation and IoT product design with Fortune 500 companies. He is a contributing member of CABA, ASHRAE, IES Education, and USGBC and a frequent lecturer on the evolving use of analytics and emerging IT technologies to foster efficiency within commercial facility design.