7 Essential Components Of A Material Handling Equipment Training Program
By Emily Newton, Revolutionized
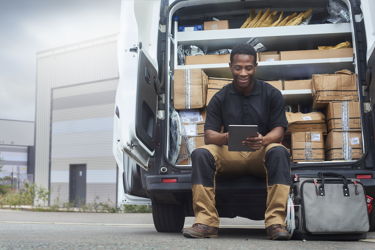
Material handling is an essential but often inefficient and hazardous part of warehouse operations. The right equipment can help overcome those issues to optimize these workflows, but this machinery is only as effective as its operators. Consequently, developing a thorough material handling equipment training program is crucial.
An effective training program will boost efficiency, reduce downtime, prevent injuries, and even mitigate labor shortages. As you develop one for your organization, here are seven essential components to be sure to include.
1. Equipment Knowledge And Operation
The most obvious thing to cover in a material handling equipment training program is how to operate the equipment in question. That starts with explaining the machine and how it works.
Employees should be familiar with their equipment. That means knowing not just what each control does but why and how it does it, as well as how the machine fits into the larger warehouse ecosystem. As more warehouses invest in automated technologies, this equipment will likely grow increasingly sophisticated, requiring more of this technical training.
Operational training should cover more than just how to drive a forklift or use a powered pallet jack. You should also teach employees specific dos and don’ts that manufacturer manuals may not come with. These tips come only with experience on the job, so sharing them with new hires in training will accelerate your workforce’s skills.
2. Safety Considerations
Your equipment training program should also cover relevant safety information. Using powered machinery instead of manually moving materials will reduce workplace injuries like musculoskeletal disorders, but this equipment has its hazards. Forklifts caused more than 7,000 injuries in 2020 alone.
Most equipment-related safety incidents stem from improper operation, so your training program should address common mistakes. That includes the importance of checking your surroundings when using equipment, how to drive vehicles safely, and any machine-specific safety protocols. You can look at past incident data to find which mistakes caused the most injuries in your warehouse before creating more targeted, relevant safety training.
Knowing how to spot and address equipment malfunctions is another important part of safety training. Develop a specific plan for recognizing and reporting hazards to include in your training program.
3. Specific Workplace Protocols
Every warehouse and loading dock is different, so each facility has unique practices and protocols to ensure everything runs efficiently. It’s important to include these workplace-specific steps in your material handling equipment training to keep your workforce productive.
Start by outlining what specific tasks and workflows you use each piece of equipment in. Restricting machine usage to these standards will minimize your risks of injury and misuse. Similarly, you should designate specific places to store equipment when not in use, as well as lockout/tag out (LOTO) procedures.
These workplace protocols should include a chain of command to turn to when something goes wrong. Employees can minimize response times when they know whom to report to for various emergencies or disruptions.
4. Maintenance Steps And Best Practices
Maintenance is another important component to include in your training program. If employees don’t know how to keep tools in good condition or spot potential issues, it could lead to costly breakdowns and lost time. Tire wear alone can impact fuel efficiency by 3%, leading to higher ongoing costs, so even small maintenance steps can have a big impact.
As employees learn to operate each piece of equipment, they should learn each one’s unique maintenance needs. These steps should include when to inspect machines, what to look for, how to perform basic fixes, and how to spot potential issues in operation.
Like workplace efficiency protocols, there should be a specific communication system for reporting maintenance issues. If workers don’t know who to talk to about problems they notice, it could lead to these issues getting overlooked.
5. Testing And Certification
A reliable material handling equipment training program covers more than just information. After teaching employees these steps, tips, and best practices, you should test their knowledge and skills. These tests will prove employees know how to manage equipment before they use it in everyday workflows and can reveal where the training should improve.
Tests should be practical rather than written so employees can demonstrate real-life skills, not just repeat memorized facts. If an employee fails a test, put them on a probationary period where they re-train and can test again later.
Only certified employees should be able to use heavy equipment. You can use ID badge-based LOTO procedures to enforce these policies, which will help improve safety and promote accountability.
6. Reassessment And Ongoing Training
Many workplaces may stop there, but if you want to get the most out of your equipment training program, you’ll take it further. After their initial training and certification, employees should have to periodically retest to maintain their certification. This will ensure they don’t forget some best practices or become complacent.
Similarly, you can establish ongoing training programs to equip employees with new skills. That could include training them to be certified equipment trainers or teaching them to be proficient in other technologies. This upskilling will help address ongoing labor shortages that 73% of light industrial organizations face.
Upskilling opportunities should be optional, but managers should take the initiative to reach out to top performers and ask if they’d be interested in them. As more employees take part in this ongoing training, you’ll end up with a more well-rounded workforce and higher engagement.
7. Collaboration And Review
Another important but easy-to-miss component of material handling equipment training is communicating with program participants. Ask workers what they thought of the training, including what they found the most and least helpful. Trainers should also ask veteran employees what they think is the most helpful to learn early on.
With these first-hand insights, you can see where your training program can improve. Making the process more collaborative also will help boost workforce engagement.
At least once a year, review your training process. Ask questions, monitor relevant KPIs, and consider how recent changes have affected equipment management outcomes for better or worse. These regular reviews will enable ongoing improvements to your training program.
Optimize Your Material Handling Equipment Training Program
Making your material handling workflows safer and more efficient means capitalizing on the right equipment. To do that, you need a reliable equipment training program.
Regardless of what equipment you use, your training program should include these seven components. If you can address all these areas effectively, you can create a safer, more efficient, and more engaged workforce.
About The Author
Emily Newton is the Editor-in-Chief of Revolutionized. She regularly explores the impact technology has on the industrial sector.