Engineering Change Orders Can Be Field Service Disasters
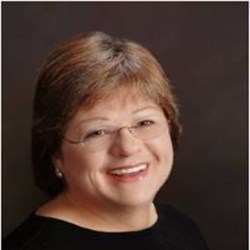
By Rosemary Coates, President and Founder, Blue Silk Consulting
Oops, did that engineering change cause a Field Service problem?
Ahhh, the darling of twenty-first-century automobiles, the Prius, caused a lot of grief for Toyota and garnered a very public apology from the company chairman, when the brakes on some cars failed. Repairs to the faulty brake systems reportedly cost Toyota US$ 2 billion*. A simple change to the design in manufacturing (before the vehicles left the production line) could have saved the $2 billion and the reputation of Toyota. When repairs must be done after product is deployed to the field, costs are magnified, and brand reputation is hurt.
Of course, when field changes are required for safety reasons, they are necessary. But too often clients make other engineering changes to drawings or the operation of new equipment without ever considering the impact or the cost to complete changes in the field. Changes are noted in engineering systems, production blueprints have to be updated on the shop floor, and Field Service has to be advised to update its records and systems. Configuration of equipment in the field has to be captured and stored in some system and config changes must be noted. This could mean making multiple entries to various software systems in engineering, ERP and CRM.
In the manufacturing world, it is common to have up to 30% of the product changed through engineering change orders (ECOs) each year. Further, another 10% may be due to something that must be changed or fixed as a field change order (FCO). Most companies don’t consider the full financial or IT impact of such changes. But world-class companies do.
World-class companies design products with Field Service in mind. This is commonly known as “design for serviceability.” In the product design process, the product goes through a complete review by the Field Service organization. In this review, all parts of the product are considered for potential repair processes, mean time between failure (MTBF), and mean time to repair (MTTR) of the total product as well as subassemblies and individual parts. Product quality may also be involved to review the overall product quality strategy. There must be final sign-off by the involved departments and partners before the product can go into production. World-class companies also develop written repair procedures and load these instructions into Field Service systems before a new product is released. The same processes are followed for new ECOs. If an ECO triggers field repairs, then additional repair instructions must be written to support the changes.
World-class companies take advantage of technology to support the change process and incorporate technology tools that empower the operation. By using technology, individuals who may be located in some other part of the world, can actively discuss, review, make decisions and communicate more effectively in real time.
It is important to keep in mind that the customer doesn’t typically pay for field changes, ECOs, or FCOs. This additional expense to your company should be included in the total cost of the product. In addition to field labor repair expense, the cost of additional inventory for repairs and logistics costs, such as global sourcing and customs duties on parts, must be considered. Product organizations will want to minimize costs to them by recommending, for example, that field inventory of old or down rev service parts be used up rather than replaced with the new improved parts. Don’t believe them; as soon as customers find out that newer better parts are available, they will demand to have new parts used for any equipment repairs.
Antennaegate
When the iPhone4 lost its signal when it was held in a certain way, Apple offered to provide a free case to every iPhone4 owner. Steve Jobs, Apple CEO, held a press conference to announce the case offering, apologized for the product failure, and explained what steps the company was taking to correct the problem.
In the meantime, the issue caused a blogging frenzy dubbed “Antennaegate.” Shares of Apple, the world’s biggest technology company by market value, fell by $1.61 to $260.09 on August 6, 2010, in response to the announcement**.
Not only was this an expensive field repair, but Apple suffered in reputation and lost significant market valuation. The people responsible for this failure left the company.
So be cautious—you may decide not to make the change based on the financial impact, including the cost to update all of your internal systems. The costs need to be balanced against customer dissatisfaction and marketplace perception.
*Forbes.com Kelsey Swanekamp, 02.04.10, 12:15 PM EST
** Bloomberg: Apple's IPhone Executive Mark Papermaster Leaves After Antenna Complaints by ArikHesseldahl. August 8, 2010, 7:27 AM PT.