Asset Performance Management And Field Service Management: The Best-in-Class' One-Two Punch
By Tom Paquin, research analyst, service management, Aberdeen
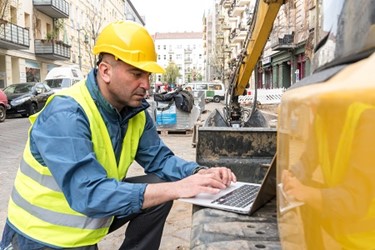
On the enterprise level, Field Service Management (FSM) software continues its march towards a state of relative maturity. Mobile penetration is near 100%, making the barrier-to-entry for powerful, lightweight tools lower than ever. Technology, of course, is never finished, so the question becomes: What’s the next frontier for service management? Routing and order is solidifying; service excellence is becoming the norm, so now is the time to optimize.
There are quite a few different routes that an organization can take to get from excellence to optimization, and I’ve talked about many of them in the past. Most are directly related to service—Fleet and routing optimization, new approached to workforce management, reverse logistics and parts management, and, of course, emerging tech. Asset Performance Management (APM), though, is not traditionally a function of service directly. Further, for many industries, it might not even be an option. For OEMs, general manufacturers, or anyone that services machinery, evaluating your current solution, and integrating it into your service software may be what pushes your business over the edge.
There’s reason to see this as a game-changer. For starters, Aberdeen’s research has shown that the #1 reason for multiple technician visits is due to the fact that the initial visit was for diagnostic purposes only. This indicates that there’s a huge opportunity to cut down on time spent on job sites by managing this tech remotely. Companies are starting to get that, as well. Our research shows that 69% of Best-in-Class organizations in the appropriate fields link their Asset Management Systems to their Field Service systems compared to 46% for all others. Furthermore, organizations that have APM and FSM working together see year-over-year technician efficiency improve twice as fast as those that don’t.
There’s naturally dozens of implementation strategies needed to do this correctly, and the barriers to entry are a bit higher than for a straight service solution (but still reasonably manageable). For most types of organizations, this requires an initial hardware investment. “Dumb” machinery won’t cut it any more; your serviceable assets need to be appropriately sensor-laden in order to collect the appropriate information. That, naturally, is the largest hurdle, and after it’s in place, you can start connecting the dots to service management.
Speaking broadly, there are three major intersection areas between service and asset management as they relate to what information can be discerned from a serviceable asset: Performance status, exception alerts, and a insights for prediction, so when planning out the connection between Service and the serviceable asset, it’s important to have a solid method of interpreting these three areas.
Let’s start with performance, which is more or less the baseline of an APM system. Understanding optimal performance of an asset, and how a firm’s machinery may be falling short, is an excellent opportunity to show the added value of your organizations’ service team. It goes above and beyond the preconceived relationship between service and the client, and lets the client know that you don’t just want their systems working, you want them working the best that they can be.
Exception alerts and predictive service go hand-in-hand, of course, and reflect the added benefit that an APM solution’s visibility offers the service firm. With exception alerts and real-time status information, technicians can skip the initial diagnostic on-site and go into an issue with a good idea of what’s wrong. Predictive service takes those status alerts and benchmarks them against historical performance to avoid service issues before they even arise. As you know—Time is money for your end users. APM and FSM together offers a way to save them both.
Asset Performance Management certainly isn’t for everyone, but if you’re in a position where you’re working with an asset that would benefit from it, there’s no excuse to be ignoring these technologies.