Artificial Intelligence In A Time Of Augmented Support
By Aly Pinder, IDC
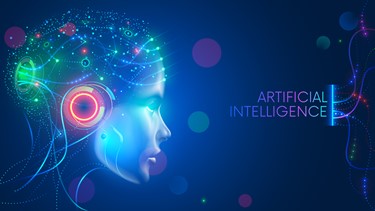
The global uncertainty impacting all of our businesses and lives at the moment has created an enormous amount of disruption. Despite the global event ravaging lives, production, and financial markets, service and field support in many cases must still go on.
For operations in the medical and healthcare industry, utilities, infrastructure, and others the ability to operate 24/7 is even more mission-critical not a nice to have. In these times when issue resolution and uptime are so critical to business, how should manufacturers prepare for the future of digital transformation within field service?
I think in the long term, many manufacturers and service organizations will re-assess their digital transformation journeys and build a strategy around intelligent service. Artificial intelligence (AI) and data-driven decision making predictively and at the point of service have the opportunity to be the enabler for the future of service excellence. In a recent IDC study, 60.0 percent of manufacturers stated in the coming 12 to 24 months AI will be 'important' or 'very important' to their company's service innovation.
I believe this number will be too low when this study is refreshed next year. The ability for AI and machine learning to enable remote service organizations to analyze vast volumes of asset, equipment, and customer data to make autonomous decisions is a game-changer; especially in this current environment where split-second decisions are needed to ensure a production line stays online, a medical testing machine is running optimally, or an airplane can operate to get supplies across the country or globe. As manufacturers and service organizations explore the promise of AI, I recommend a few areas to be considered:
- AI should augment and aid the field service technician. Too much effort is paid to how AI will be a doom and gloom scenario. AI is here today, and its impact is more likely to be accretive to human field service teams and not competitive. Removing repetitive or administrative minutia must occur to ensure technicians can focus on delivering value to customers. AI also can provide technicians with the right answer to a problem faster and on-demand. As machines, products, customers, and equipment create more data having the ability to quickly get to the right answer will be the differentiator for service and ensure technicians can resolve issues in a timely manner.
- Make sure your technicians know their value to the company, customers, and service quality. Technicians are often said to be the lifeblood of organizations or the embodiment of the brand on the product or van delivering service. Unfortunately, this message often gets lost or doesn’t reach the field team it is meant to elevate. As organizations evolve digitally and automate more business processes, technician value to the customer and the service experience must not be minimized. Technicians need to know AI and other technology capabilities are meant to augment not replace valuable field service work.
- Ensure data and intelligence are accessible on-demand. Over the last few years, there has been a wave of hiring with regard to data scientists and analysts. These experts get to mine through data and provide some great insights that lead to innovations and transformation. The problem I see is data shouldn’t be kept in the data scientist wing of organizations. Organizations need to be able to analyze information and make important insights available across the organization at the time it's needed. This takes a high level of sophistication, but this is the value of the data.
Service and quality service are front and center in these challenging times. The ability to ensure equipment is operating to meet critical production targets has never been more important. For this reason, service organizations must make the right decisions to solve issues before failure. The impact of AI and other advanced data capabilities has the opportunity to accelerate digital transformation and service excellence for manufacturers and service organizations today and into the future.
About The Author
As Program Director, Service Innovation & Connected Products, Aly Pinder Jr leads IDC research and analysis of the service and customer support market for the manufacturer, which includes topics such as field service, warranty operations, service parts management, and how these service areas impact the overall customer experience. Mr. Pinder Jr. is also responsible for research which aids manufacturers as they evaluate innovative technologies like 3D printing for service operations, augmented and virtual reality in field support, and the use of IoT and advanced analytics for remotely monitoring and managing assets. Mr. Pinder Jr. establishes a roadmap for the manufacturer to better understand how technology can transform service and support functions to drive exceptional customer experiences and customer value, profitable revenue growth, and improved efficiency in the field.