A Look At The Technologies That Will Help Mitigate Today's Field Service Problems
A conversation with Jim Dempsey, Panasonic
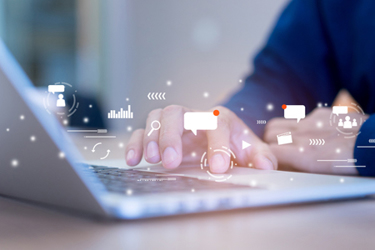
Jim Dempsey is National Sales Director at Panasonic where he leads a team focused on developing and managing Panasonic's channel and technology ecosystem. His team’s primary focus is on growing Panasonic’s Android line of rugged handheld and tablet products and the reseller channel supporting those products. Jim took time to speak with Field Technologies Online about the challenges he sees in the field service industry, barriers to the adoption of technology, and more.
Q: What challenges do you see in field service workforces today?
Dempsey: In this digital age, a lot of enterprises are still using manual methods to manage the bulk of their field service tasks rather than automated software solutions. As you can imagine, this creates a lot of unforeseeable errors and delays which translates to negative customer experience. Some customers might receive late appointments or worse, the technician might not end up showing up at all. Frustrated customers will soon start looking elsewhere.
Enterprises widely recognize that automation can dramatically improve the efficiency of their field workforce, which in turn helps to minimize customer downtime and increase customer experience. With edge technologies such as AI and IoT, companies can track field technician’s location, schedule tasks with ease, and answer customers’ inquiries in real-time using chatbots and automated online tools. These edge technologies are made possible and work most efficiently with the right mobile devices. However, deploying many devices across an enterprise is certainly no easy task. They need the support and services to future proof their operations by leveraging the capabilities of modern mobile devices. If an enterprise relies on a legacy system, it needs to find ways to integrate software seamlessly with their existing IT infrastructure and be able to upgrade it to provide the maximum efficiency for their field workers.
Q: What are some of the barriers to technology adoption?
Dempsey: Specifically for workers using handheld devices on the job, Windows CE and Windows Mobile end-of-life is forcing some companies to have to figure out what operating system they will go with next, Android being the most common option. Though some companies struggle with misconceptions around Android not being secure or reliable. Additionally, rewriting Windows CE applications can be very costly and time consuming, so many enterprises choose to use what they already have. However, with the right IT services, software, and support, enterprises can successfully transition to a new operating system, rewrite applications, configure device settings and manage its entire mobile workforce in a shorter time and at a much lower cost.
Q: What are the technologies and solutions field service and logistics managers need to create safe working environments?
Dempsey: There are three that come to mind – thermal imaging, drones, and mobile solutions.
- Thermal Imaging: It’s difficult for technicians to perform diagnostics on a problem happening out in the field when oftentimes electrical and mechanical systems are hidden behind large motors, plastic encasing, or other machinery. To tackle this, thermal imaging helps technicians to locate the source of a problem and eliminate potential operational failures. When field technicians are equipped with mobile solutions such as a rugged tablet, they can scan the area and identify any heat or leak risks.
- Drones: According to Frost & Sullivan, drone adoption is expected to grow from 2.4 to 2.9 million units by 2023. In today’s environment, drones have been useful for their ability to maneuver around and above otherwise difficult to reach areas and communicate that information back to field workers on the ground. When field technicians are on-call in remote locations, drones can help eliminate the need for workers to physically access potentially dangerous areas. Drones can also help to predict potential safety hazards before sending technicians on-site or reduce the number of workers in an area as part of safety guidelines in our new norm. Data-powered drones and mobile technologies enable real-time visibility and foster smarter decision-making.
- Mobile Solution: More and more, we are seeing field services companies adopting Android-based rugged mobile devices for their technicians. At Panasonic, we recently launched the TOUGHBOOK A3 Android tablet and productivity+, a suite of software and services for Android users. The A3 is best designed to address field technicians’ needs for portability and wireless connectivity when working remotely. The tablet features an outdoor viewable and glove-touch sensitive screen, ergonomically designed buttons for ease of use, and dual hot-swappable batteries. For wireless connectivity, the TOUGHBOOK A3 has near-field communications (NFC), Wi-Fi, Bluetooth, and 4GLTE cellular.