Slim Pickings
RF-enabled data collection over a WLAN helped $500 million Bear Creek thin its order fulfillment processes.
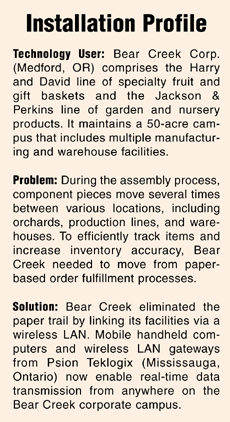
Accurate information is crucial for avoiding conflict. It's as true in business as it is in life. When messages are garbled, misinterpreted, or misrouted, problems occur. Your staff becomes angry because of a rumor that the company is considering five hourly layoffs. (In reality, a manager was overheard commenting about a five-hour layover between flights.) Your customer is upset because four cases of widgets were missing from yesterday's shipment. (A data entry error caused several pallets to be placed in the wrong warehouse location and, therefore, missed during picking.) There probably isn't much you can do to prevent "five-hour layover" from devolving, after several whispered conversations, into "five hourly layoffs." But, you can do something about those missing widgets. Start by reducing the manual processes that create communication errors. Finish by opening wireless paths for real-time data transfer and systems updating.
At Bear Creek Corp. (Medford, OR), a mail-order distributor of specialty gift and garden products, the move to wireless order fulfillment processes wasn't triggered by any obvious crisis. Manual cycle counts of SKUs (stock keeping units) revealed that materials inventory accuracy, for example, wasn't horrible - in fact, it was more than 90%. Still, there were noticeable inefficiencies. Hard to miss were two inordinately large workforces - one devoted to manual data entry, the other to solving problems associated with miskeyed inventory transactions, lost paperwork, and the absence of bar code scanning. Plus, customers in today's fulfillment landscape expect short turnaround windows. Companies that regularly meet those demands have long since surpassed the 90% threshold and attain near 100% inventory accuracy levels. So, to tighten its internal processes, Bear Creek looked to link its back end systems to a WLAN (wireless LAN). Connected to the LAN are RF (radio frequency)-enabled handheld devices used to collect data on Bear Creek's shop floors and in its warehouses.
Narrow Band, Thick RF Coverage
Bear Creek distributes two specialty product lines through mail-order, retail, and wholesale channels. The Harry and David line, noted for its core offering, the Royal Riviera pear, includes gift boxes and baskets of fruit, cheese, nuts, and chocolate. The Jackson & Perkins brand offers garden and nursery items - most notably, a select line of roses. Although both divisions outsource some of their component pieces, the core products for both are still homegrown - literally. Jackson & Perkins maintains rose fields near Bakersfield, CA, while Harry and David maintains fruit orchards in Oregon's Rogue Valley.
A wireless infrastructure was particularly well suited for Bear Creek's manufacturing and warehouse environments. Because the component pieces of any Bear Creek shipment are mostly perishable items, the 50-acre, multi-facility central campus includes several refrigeration and freezer areas. Located inside manufacturing facilities are smaller units used for short-term storage during assembly. Larger refrigerator and freezer buildings provide long-term cold storage. Non-refrigerated areas include assembly floors, as well as warehouses that house packaging materials - cardboard, baskets, foam, ribbon, and so on.
The itinerary for a perishable item might include several truck rides around campus as the item is moved into and out of cold storage during manufacturing, staging, and loading for delivery. Tracking that item as it passes through various indoor and outdoor checkpoints and differing storage environments requires the kind of data collection flexibility that wireless networks and wireless handheld devices provide. For that purpose, Bear Creek uses approximately 80 truck-mounted data collection terminals and more than 40 handheld devices, all from Psion Teklogix. It also uses Psion Teklogix wireless LAN gateway equipment.
Bear Creek was particularly attracted to the Psion Teklogix system because of its narrow band technology, which delivers strong signal strength. "Because we have a lot of buildings, some of which are made of thick concrete, we needed a system that could guarantee wireless coverage across our campus," says Ric Sharp, Bear Creek's director of engineering. "Had we gone with lesser signal strength and higher speed, we would have had to install many more gateway stations around picking areas. With the stronger signal strength, we actually have more buildings than gateways, with a gateway in one building able to cover nearby buildings."
WMS Handles Wireless Transactions
The mobile data collection terminals on the manufacturing and warehouse floors communicate over the wireless LAN to multiple, integrated back end systems. The central WMS (warehouse management system), CatalystCommand from Catalyst International, resides on an IBM RS/6000 server. From there, it interfaces with Bear Creek's purchasing, manufacturing, and order entry systems. "The Catalyst WMS sends inventory transactions to the manufacturing system and receives purchase orders from the purchasing system," Sharp explains. "It also receives customer orders from the order entry system and uses them to generate picking orders from the finished goods warehouse."
The journey of raw materials - cocoa butter, for example - demonstrates why the back end system must be able to communicate with wireless devices scattered across the campus. As a shipment of cocoa butter is unloaded at a freezer warehouse, an employee uses a handheld device to enter receipt of the shipment into the WMS. At each subsequent step, employees in various locations do inbound or outbound WMS inventory updating from wireless devices. When more cocoa butter is needed in the production of truffles, for instance, an employee in a food processing facility enters an outbound order into the WMS, which generates a pick directive. The picked cocoa butter is loaded onto a truck and transported across campus. After production, the truffles are typically placed in boxes for bulk storage and re-entered into the WMS. This time, they are transported to a 34-degree cold storage building. Eventually, they are picked from cold storage and sent to a work-in-process area, where they are packaged as finished items. After that, it's back to a freezer warehouse. When the time comes to ship the product, it gets pulled from the freezer, put on a truck, destaged, and transported to the shipping dock. "In the old days, all of those inventory transactions - from receipt to shipment - were logged on paper forms that forklift drivers and people on the shop floors would write on," Sharp explains. "Those forms were periodically collected during the day, and we had 20 to 25 people doing data entry to get them into the system. There were lots of opportunities to lose paper and to make data entry and data interpretation errors."
It's About Time, It's Always About Time
With the wireless system in place, inventory accuracy at Bear Creek has skyrocketed - from a little more than 90% to 99.5%. Real-time data communication has also contributed to increased productivity and efficiency on the warehouse floor. "The people doing picking and packing are receiving new directives as soon as they finish an activity," says Sharp. "Those directives also ensure that products and materials are put away in a consistent manner, making picking much more efficient."
Real-time communication also means that Bear Creek can respond to problems more quickly. Previously, shortages in manufacturing materials or finished goods weren't always reported in a timely fashion. "Now, as picking is occurring, updates to the system immediately indicate when stock is running low. That allows our resource planners to respond proactively," Sharp says.
Finally, reductions in labor, time, and errors have meant reductions in spending. Bear Creek measures the efficiency of its materials usage by considering materials management costs relative to the number of units manufactured. "In only the third year with the wireless system, that figure improved by 10%," Sharp notes. "The implementation of the WMS, plus process changes in our approach to materials handling, contributed to savings of more than a million dollars."