Shop Floor Shake-Up
A third-party package will help your ERP (enterprise resource planning) system manage inventory. But, maybe the best solution can be found within your company.
Small Manufacturers Have Big Storage Needs
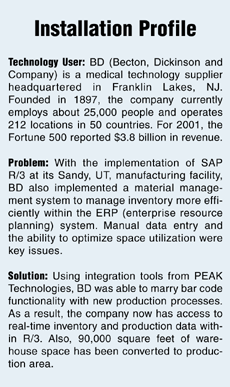
In November 2001, Lee Hudson had new marcH-ing orders. For 30 years - predating PCs - Hudson has served medical technology supplier BD (Becton, Dickinson and Company) in various IT and manufacturing capacities. His new directive is to play matchmaker to these sometimes reluctant participants - marrying IT with manufacturing to gain efficiencies and improve the bottom line. And while his new title, corporate IT business integrator for manufacturing, doesn't exactly roll off the tongue, it carries the backing of BD's CIO.
The union of IT and manufacturing is well established at the company's manufacturing facility in Sandy, UT, and is in its honeymoon stage at the company's other manufacturing and distribution facilities. In addition to diagnostic media and laboratory supplies, the $3.8 billion BD is one of the largest manufacturers of medical equipment in the world, with product lines ranging from syringes to scalpels to anesthesia systems. The Sandy facility handles the production of some of the company's most popular medical devices. Because an influx of IT on the floor is coexisting happily with the manufacturing processes at Sandy, BD will look to tie similar knots at its six other large production facilities in the United States and at dozens of sites worldwide.
The reasons that make the Sandy facility such an interesting test case for BD and other manufacturers are twofold. First, the Sandy facility, like many manufacturing sites, is running SAP R/3 as its ERP (enterprise resource planning) system. And like many manufacturers, BD found the inherent inventory management capabilities of the R/3 system to be cumbersome compared to the functionality that was required. Second, BD's solution to this problem is not like that of many manufacturers.
Stepping Beyond Current ERP Functionality
Because BD is manufacturing medical equipment and not plastic toys, the company operates in a regulated, batch-managed environment. For a toy manufacturer, a shipment of plastic resin is considered just one part number in the production process. When the resin runs low, another shipment is ordered. For BD, it's much more complicated. Each shipment of resin must be subdivided by the number of batches that will be consumed. This allows the company to trace the raw materials and resulting components of the products that it produces. But, treating one shipment of resin as thousands of individual parts puts an enormous transactional strain on the ERP system. "At a high level, the R/3 system is very good," says Hudson. "But, we're in a highly repetitive and regulated manufacturing environment where we make millions of products each week. It becomes a real problem when you have to manually enter tens of thousands of transactions into the ERP system in order to maintain it."
It's at about this time that many companies turn to a third-party inventory management system - maybe even a system that is designed for this vertical market. It tracks the inventory as materials come in the door and as they are doled out to production. It's interfaced with the ERP system and also communicates with suppliers. But, along with additional costs, it's also another system for the IT department to maintain.
Instead of changing software to match its business processes, BD changed its processes to take advantage of the software it had in place. The company's new strategy borrowed heavily from the Kanban (pronounced kahn-bahn) system of manufacturing that was developed in Japan at Toyota Motor Company. Taken from the Japanese word for placard (this will be made apparent later on), BD "Americanized" this form of JIT (just-in-time) manufacturing to better fit both the company and its suppliers.
Don't Let Suppliers "Push" Inventory On You
While most supply chains have materials being "pushed" at manufacturers based on production schedules and sales forecasts, the Kanban system is all about "pulling" materials into the manufacturing process. In the most simplistic of terms, it can be equated to refilling the staples of most kitchen cabinets. Check the amount of ingredients on hand, make a list, have a grocery store fill an order, and repeat the process in timely intervals. "It's all about getting the appropriate quantity of supplies for the rate in which you consume them," says Hudson. And BD must accomplish this task in a regulated environment.
One particularly challenging aspect of pulling inventory into the manufacturing process is training suppliers that are used to pushing inventory. At BD, these suppliers are comprised of internal vendors (BD manufactures component parts within the Sandy facility) and external vendors (components supplied from outside BD). Instead of using production schedules and forecasts as a basis for delivery, the Sandy facility maintains a safety stock of each component. The inventory is delivered into production from this safety stock as needed until it is depleted to the point where it makes sense to order additional stock. "If a supplier manufactures component parts in runs of 300, then we'll wait until we at least use 300 of those parts before contacting the supplier," comments Hudson. "Then, we'll take that minimum amount into inventory to reach our safety stock level and then repeat the process."
Inventory is used and replenished on a close to real-time basis. For internal vendors, this adjustment was simply part of the company's new business processes. For external vendors, it meant shipping more frequently and in smaller quantities. In addition to keeping BD as a customer, complying with the Kanban system has other advantages for external suppliers. "We commit to a certain amount of annual business with our external suppliers. But, we don't commit to delivery dates on that business," says Hudson. In the end, the suppliers get a certain level of comfort that comes from having a committed large customer. This tends to offset the discomfort of receiving a BD order on Monday that requires delivery by Wednesday.
Bar Codes Connect R/3 To Item-Level Management
The most obvious change in BD's manufacturing processes was not in rewriting code, but in the addition of plastic totes, called Kanbans, at BD. Between the Sandy facility and its internal and external suppliers, 39,000 Kanbans are used to track the flow of materials into and out of the production process. Different Kanbans have been designed to hold different component parts, but every Kanban contains a bar code that acts as a unique ID or license plate. "The Kanbans are filled by suppliers and entered into production, where the components are used. The Kanbans are then sent back to suppliers where they are refilled," explains Hudson. To accommodate traceability requirements, the unique ID is used to track the inventory as it moves from one area of the plant to the next. "When we issue a Kanban into production, for instance, we scan the production order and the unique ID of the Kanban," Hudson adds. "It's that simple." According to Hudson, the Kanbans never stockpile on the production floor. No more than two Kanbans are allowed in the same production area. When the contents of one are consumed, the Kanban ID is scanned and this triggers the release of another Kanban to the production floor.
The new "lean" inventory and materials tracking system in place at Sandy was written by the in-house staff at BD, with an assist from PEAK Technologies. The manufacturer relied on PEAK's S/3 Interface to connect its now bar code-based processes with SAP R/3. The GUI (graphical user interface) configuration tool that makes up the PEAK S/3 Interface allowed BD to create messages and prompting sequences that were tailored to the company's business processes. The PEAK S/3 Interface made possible the transfer of data between the R/3 database and the bar code scanners.
More Transactions With Less Overhead
The introduction of new bar code-based manufacturing processes has allowed BD to slash the inventory it carries to just the most basic level of safety stock. The company is also maximizing the SAP system that it implemented four years ago. By reducing on-hand inventory, the company freed up 90,000 square feet of what used to be part of the warehouse operations at the Sandy facility. That newly available space has since been converted to a production area, increasing the plant's overall output without enlarging its footprint.
As for the R/3 system, it's handling more transactions with less overhead than BD thought possible. Some manufacturers manually post all transactions to R/3 once per day as a batch process. The system reads this as just one big transaction. At BD's Sandy facility, about 36,000 transactions are automatically posted to R/3 each month. "We're not manually entering data into the R/3 system. We have real-time granular data, and we've expanded our production capacity," states Hudson. "SAP's a good system. We're just making it better."